White Paper
CNC Machining Starter Guide
An introduction to basic CNC machining terms and definitions
What's Covered
- CNC Machining Defined
- Glossary of Terms
- Design Process
- Types of CNC Machines
- CNC Tooling
- Common Materials
- Advantages
- Applications
Introduction
We’ve come a long way since shaping metal with a hammer. CNC machining revolutionized the manufacturing industry by automating the processes of shaping and cutting various materials. From design to assembly, CNC machining allows manufacturers to create products with speed, quality, and precision.
CNC Machining Defined
A computer numerical control (CNC) machine is an automated machine that performs tasks programmed by digital software. The machine processes materials according to design specifications uploaded from the software, all without a manual operator. Precision CNC machining is the use of CNC machines to turn a raw piece of material into a desired (and precise) shape. With CNC machining, knowledgeable workers can operate a fleet of machines by utilizing computer software.
CNC machining is subtractive manufacturing. As opposed to building a product by adding material or parts, CNC machines remove material from a workpiece through various methods (like cutting and grinding) to shape the source into a final design.
Glossary
Here are common terms associated with CNC machining:
Axis – Direction of movement or plane of motion; most CNC machines move tools or workpieces in at least three directions: left and right (X-axis), forward and backward (Y-axis), and up and down (Z-axis).
3-Axis Machine – A 3-axis CNC machine operates along three axes (X, Y, and Z). Typically, the workpiece is held onto a table that moves along the X and Y axes while a cutting tool moves along the Z axis.
4-Axis Machine – A 4-axis CNC machine has the capabilities of a 3-axis machine, but it also can rotate along one of the axes (this rotary axis is often called the A-axis) . With this additional rotary axis, the machine can flip over a workpiece and remove material from another side.
5-Axis Machine – A 5-axis CNC machine can work on five sides of a workpiece at one time. It has the three main linear axes (X, Y, and Z) and can operate two additional rotary axes (A and B).
6-Axis Machine – A 6-axis CNC machine can work on six sides of a workpiece at one time. It has the three main linear axes (X, Y, and Z) and can operate three additional rotary axes (A, B, and C).
Automatic Tool Changer – Also known as ATC, this is a system that automatically changes the tools in a CNC machine to fit the task without the need for human interaction.
CAD – Computer-aided design; engineers use CAD software to design 2D and 3D models.
CAM – Computer-aided manufacturing uses software to define toolpaths and assist in the manufacturing process.
CNC – Computer numerical control; a CNC machine utilizes a computer programmed with numerical commands (G-code) to move.
Feed Rate – How fast the tool moves on any axis. This is dependent on the depth of cut, tool geometry, the material being machined, and the desired surface finish.
G-Code – The most widely used CNC programming language, G-code uses axis points and commands to tell a machine how to move and perform functions. Think of G-code as the directions for a map route that your machine will follow.
M-Code – Machine code; the language that directs miscellaneous machine functions like starting and stopping specific actions or programs, as opposed to commanding axis motion.
Measurement or Inspection Tools – A micrometer incorporates a calibrated screw to achieve the accurate measurement of machining components. A caliper is an instrument used to measure the dimensions of an object.
CNC Parts
Different types of CNC machines have varying components depending on the machine type. Most CNC machines have the following parts:
Bed – The support for entire machine; the bed’s structure depends on the type of CNC machine, but it is generally a box structure.
Control Panel – The brain of the CNC machine; it contains the input device, the display unit, and control buttons to help operators manage the machine.
Cutter – The machining tool used to remove material from the workpiece.
Spindle – The rotating axis that drives the motion of the workpiece or tool.
Tool Holder or Adapter – These hold the cutting tools and secure them to the CNC machine spindle. They are usually made of hardened steel or other robust materials. There are a variety of tool holder types (collets, chucks, etc.) to accommodate various tool sizes and shapes.
Vise – The device that grips, holds, or clamps the workpiece in place to keep it still during machining operations.
Workpiece – The object or material that is being machined.
Design Process
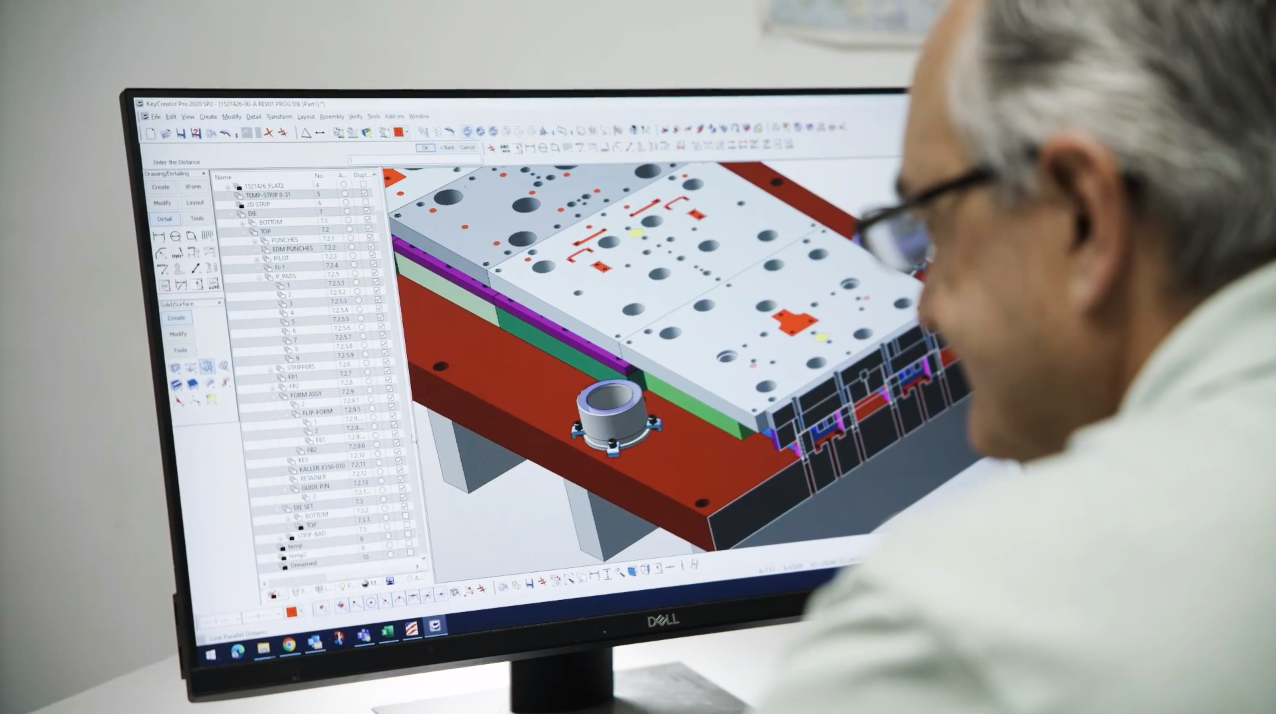
CNC machining starts with a design. In some cases, a client creates the design and delivers a digital file to the manufacturing partner. In other cases, the manufacturer assists with creating the original design while collaborating with the client.
Design software
Computer-aided design, or CAD, software is used to build a model of a design. The file holds the information about the dimensions and form of the object. CAD allows 2D and 3D models to be created more quickly, shared, measured, modified, and stored. Computer-aided manufacturing (CAM) software gives machines instructions on how to execute the design. Once a design is approved, CAM software translates the CAD file into instructions using G-code (which directs the motion of a CNC machine) and M-code (which controls the operations not involving motion). If CAD is a path, CAM is the set of directions on how to get through the path to the other side.
Design Execution
The CAD file holds all the critical design information, allowing everyone involved to easily review, simulate, and modify designs as needed before a real-world part is even created, helping cut down setup time and scrap. Once the program is ready, a machinist transfers the CAM file to the CNC machine. Then, a setup machinist prepares the machine to run the program, and an operator prompts the machine to execute the design.
CAD
Creation, modification, and analysis of a design. Think of CAD as a map.
CAM
The use of software to translate a CAD file into a digital tool path and set of instructions.
CNC
The automated control of machining tools to execute a CAM program.
Types of CNC Machines
CNC machines (and their creations) come in all shapes and sizes. Some are so small they can fit on a woodworking table in the garage of a house. DIY crafters, small business owners, or any machinist can use them to make jewelry, furniture, or small design projects. They can also be used to build parts and tools that are part of larger projects. On the other hand, some CNC machines are so big they are the size of a house and weigh up to about 50 tons. Larger CNC machines can also build small items (and are particularly useful when those small items need to be mass produced), but they are also necessary to work on larger, heavier workpieces.
Lathe and Turning Centers
A CNC lathe or turning center cuts workpieces while they are rotated, with the tools remaining fixed. They make fast, precise cuts, and they generally have fewer axes than milling machines. CNC turning centers and lathes are usually used to create cylindrical parts due to the way the machine operates. They are often used to build prototypes, spacers, or shafts below 2.5 inches. They are often more compact than CNC milling machines.
Milling
With a CNC milling machine, a block of material remains stationary while tools shape or cut the material. Milling centers either come with an automatic tool changer or a machinist manually swaps out tools. They all have a stationary workspace that secures what’s being machined to minimize its movement. Horizontal milling machines, which have a spindle that is mounted horizontally, are usually used to create grooves on a machined piece.The machine's design allows for removed material to fall off the workpiece without interfering with the tool. Vertical machining centers can be used for drilling and plunging cuts. They typically have 3 to 5 axes and are large compared to other tools.
Plasma Cutter
A plasma cutter blows gas at a high speed from a nozzle, coinciding with an electrical arc that turns the gas to plasma. The hot plasma melts the material being cut and blows away molten metal.
Laser Cutter
CNC laser cutters direct a laser beam at the source material to cut, engrave, mark, etch, and, in some cases, weld materials.
Electrical Discharge Machines
Electric Discharge Machining (EDM) uses electrical discharge or sparks to create a desired shape from a source material. A series of recurring electrical discharges between two electrodes remove material from the workpiece.
CNC Tooling
CNC machine tools are the various cutting tools and accessories used to remove material from the workpiece to shape and finish the product. CNC lathes use stationery tools and move the workpiece into the tools to remove material. CNC milling machines move tools into a workpiece to make cuts. These tools come in different types, each designed for specific tasks and materials. The wide range of tooling options allows for top-notch performance and customization of the end products.
Various tooling options exist because of the diverse range of materials and machine options available. Different materials require different tooling to maintain tool life, precision, and performance. As technology advances so will our tooling options.
Turning
Turning tools work with a lathe that rotates the workpiece while the tool shapes it according to design instructions. Common turning tools include boring, chamfering, knurling, parting, and facing tools.
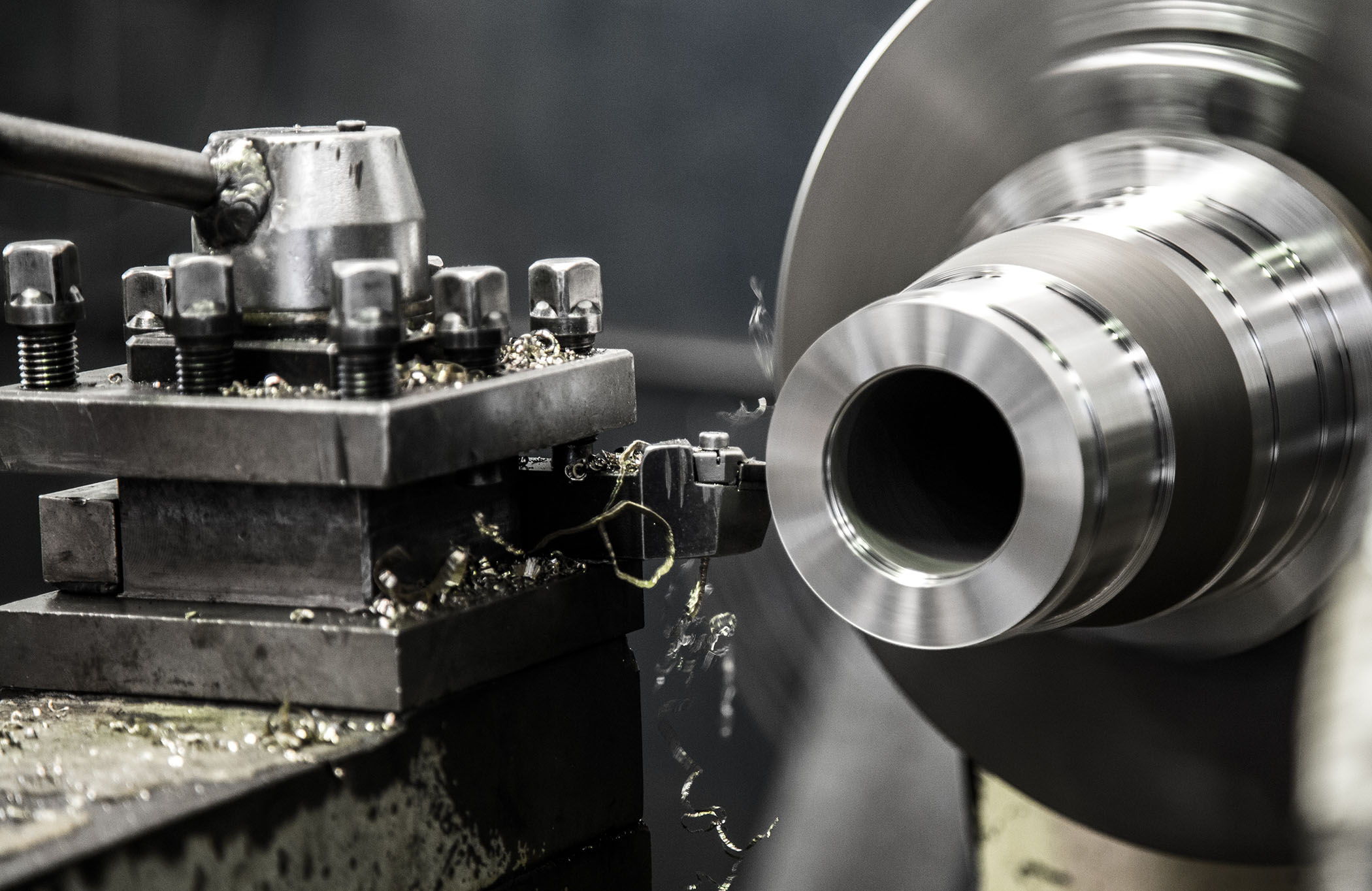
- Parting Tools:
- Material: Usually made of carbide, ceramics, or high-speed steel (HSS).
- Function: To perform cutoff operations in the machining process.
- Variety: Various tool geometries and coatings for turning different materials.
- Boring Bars:
- Material: Typically made of carbide or HSS.
- Function: Used to enlarge and refine existing holes.
- Variety: Various sizes, tool geometries, and coatings for different bore diameters and depths.
Drilling
CNC drill bits are cutting tools that come in three varieties: center, ejector, and twist. Center drill bits create small, precise spots on the workpiece, which can then be drilled into with a twist drill bit. Ejector drill bits are used to drill deeper holes.
- Drill Bits:
- Material: Made of HSS, cobalt, carbide, or diamond.
- Function: Used for creating holes in workpieces.
- Variety: Various point geometries, flute designs, and coatings for drilling different materials.
Cutting/Milling
CNC cutting tools remove material from a fixed workpiece, typically by moving in a circular motion. Cutting tools must be harder than the material of the workpiece being cut. Common cutting tools include end, slab, face, hollow, and thread mills, as well as fly cutters, drill bits, reamers, and gear cutters.
- End Mills:
- Material: Typically made of high-speed steel (HSS), cobalt steel, or carbide.
- Function: Used for cutting slots, profiling, and contouring in various materials.
- Variety: Different flute shapes, coatings, and helix angles are available for specific materials and cutting conditions.
- Milling Cutters:
- Material: Made of carbide, HSS, or high-performance materials.
- Function: Used for a variety of milling operations, such as face milling, slotting, and profile milling.
- Variety: Different cutter types (end mills, ball nose cutters, etc.), insert styles, and coatings for diverse milling tasks.
- Reamers:
- Material: Typically made of HSS or carbide.
- Function: Used to accurately size and finish drilled holes.
- Variety: Different flute designs, coatings, and tolerances for achieving precise hole dimensions.
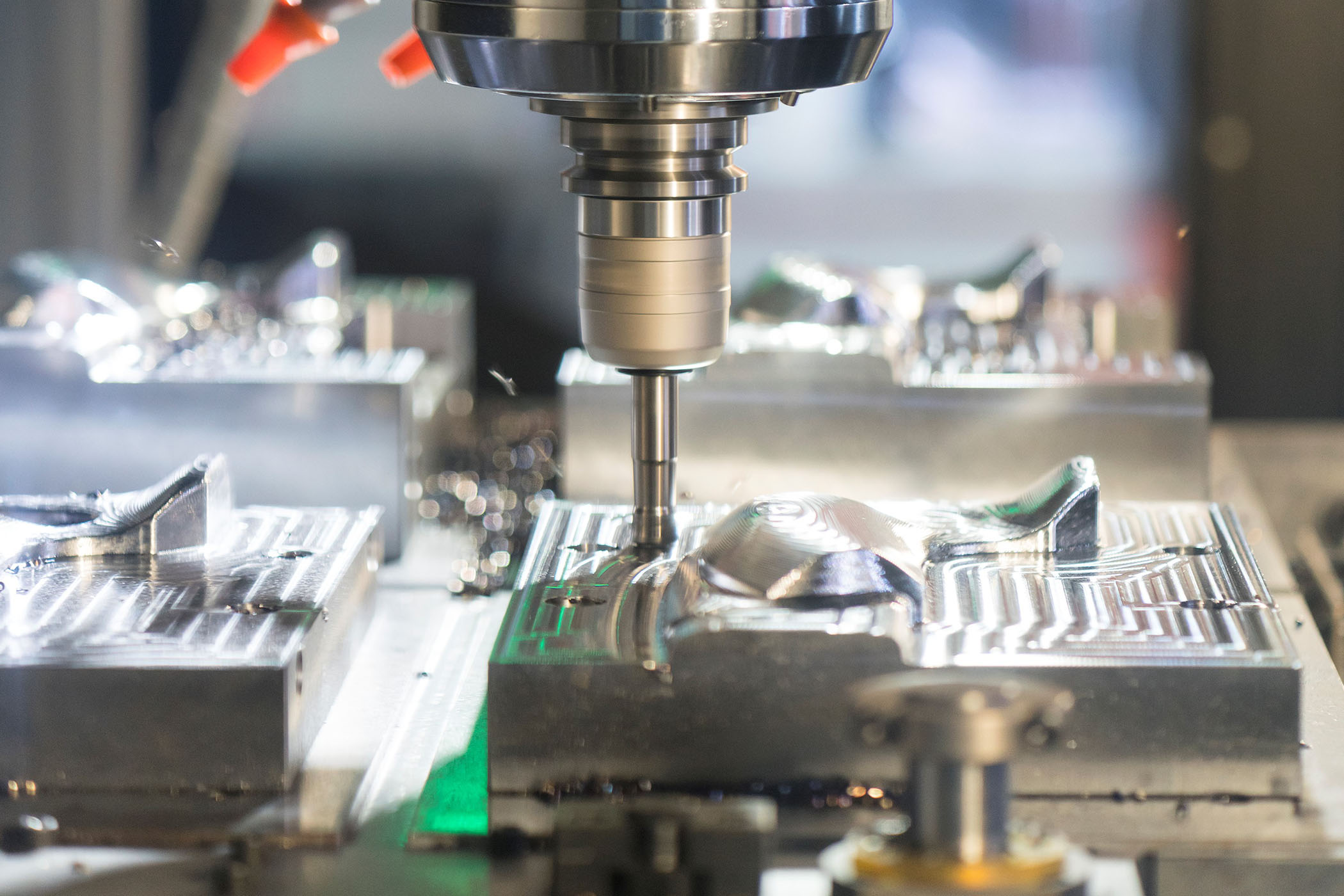
Grinding
CNC grinding involves removing material from a workpiece using a rotating, abrasive wheel. The grinding wheel is the tool on the CNC machine.
- Grinding Tools:
- Material: Commonly made of aluminum oxide, silicon carbide, cubic boron nitride, and diamond.
- Function: Removing material from a workpiece.
- Variety: Surface grinding, cylindrical grinding, and precision grinding.
Threading
CNC threading is the process of cutting spiral groves or threads on a cylindrical workpiece using taps and dies.
- Taps and Dies:
- Material: Usually made of high-speed steel or carbide.
- Function: Used for threading operations to create internal and external threads.
- Variety: Different thread sizes and pitch, as well as tap designs for various materials.
Common materials
Any material can be effectively machined — what may change with the use of a CNC machine may be the size of the material, processing speed, rigidity, cutting tools, coatings, and the specific technology used to process the material. Some characteristics engineers, designers, and manufacturers keep in mind when determining which material to use for their projects are how the part or item they are creating will be used, any temperature requirements, and how heavy or light it needs to be. These are some of the most common materials used in CNC machining:
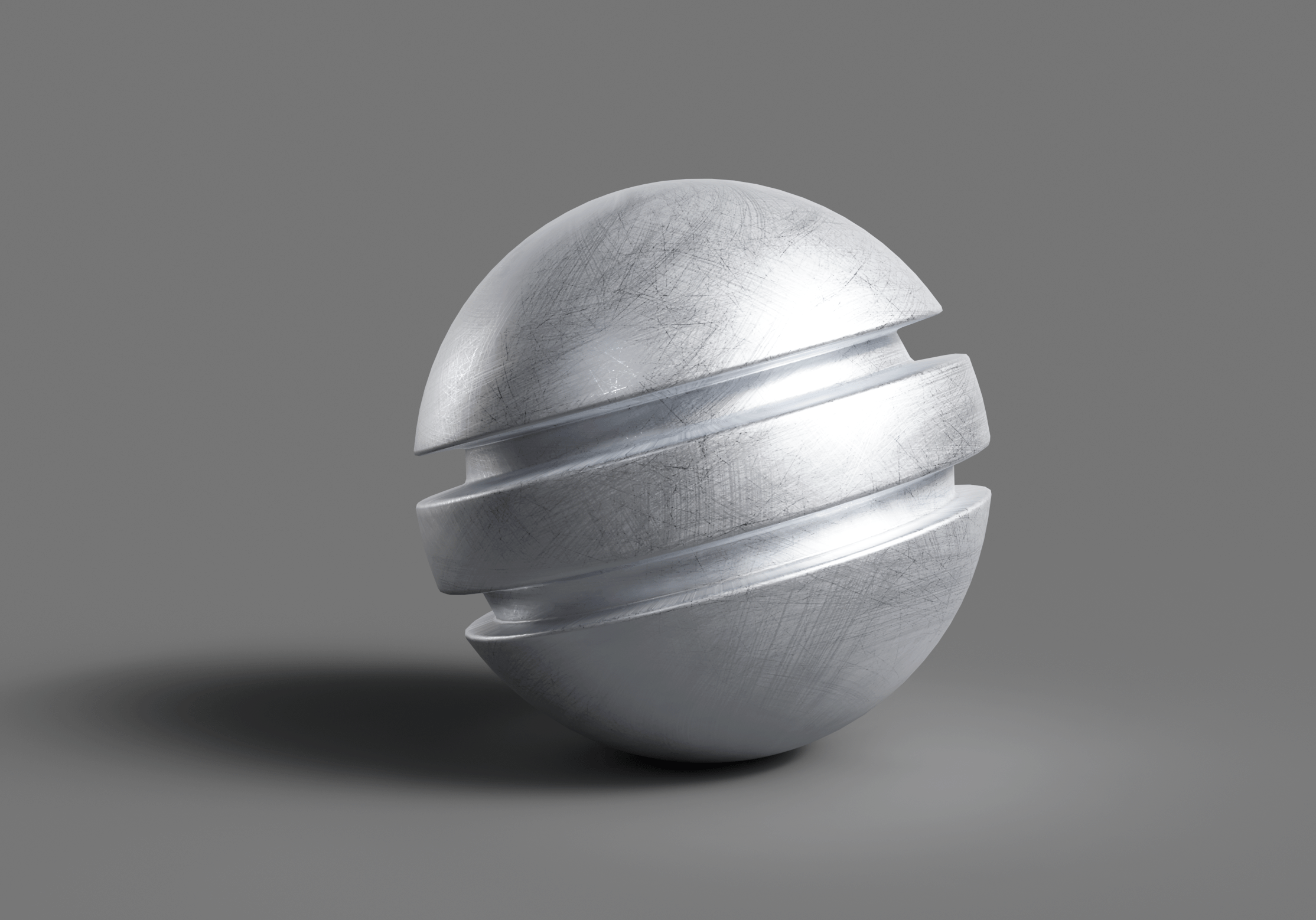
Aluminum
Aluminum is commonly used in CNC machining because the metal is lightweight, resistant to corrosion, strong, and durable. Its applications are far-reaching, but aluminum is frequently used in the transportation, aerospace, and construction industries. Aluminum 6061 is one of the most common aluminum alloys used in CNC machining because it is highly weldable, versatile, and easy to machine, and it tolerates different heat treatments. It is frequently used in the construction of aircraft structures, automotive parts, bicycle frames, and computer parts. The strongest commercially available aluminum alloy is aluminum 7075, which is frequently used for aerospace and aircraft component parts subject to high stress.
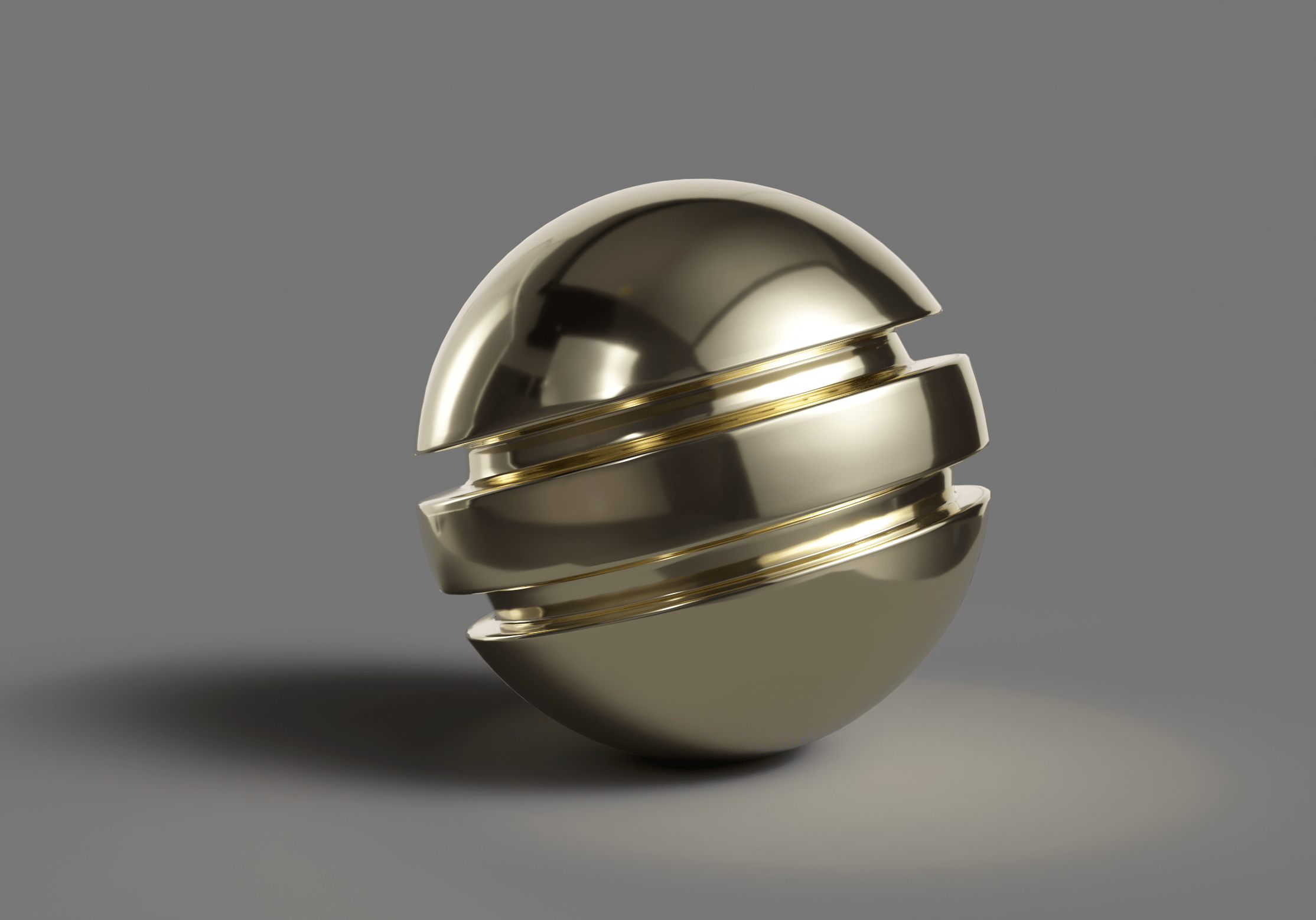
Brass
Brass is an alloy of copper and zinc, and it is considered one of the easiest materials to machine because of its malleability, general softness, and low melting point. It is more durable than aluminum and holds up well in more stressful environments over time. Brass can be manufactured with a very small tolerance making it a perfect fit for parts and components that require a high degree of accuracy. Brass is often used to make tools like screws and rivets, musical instruments, medical parts, and electronic components.
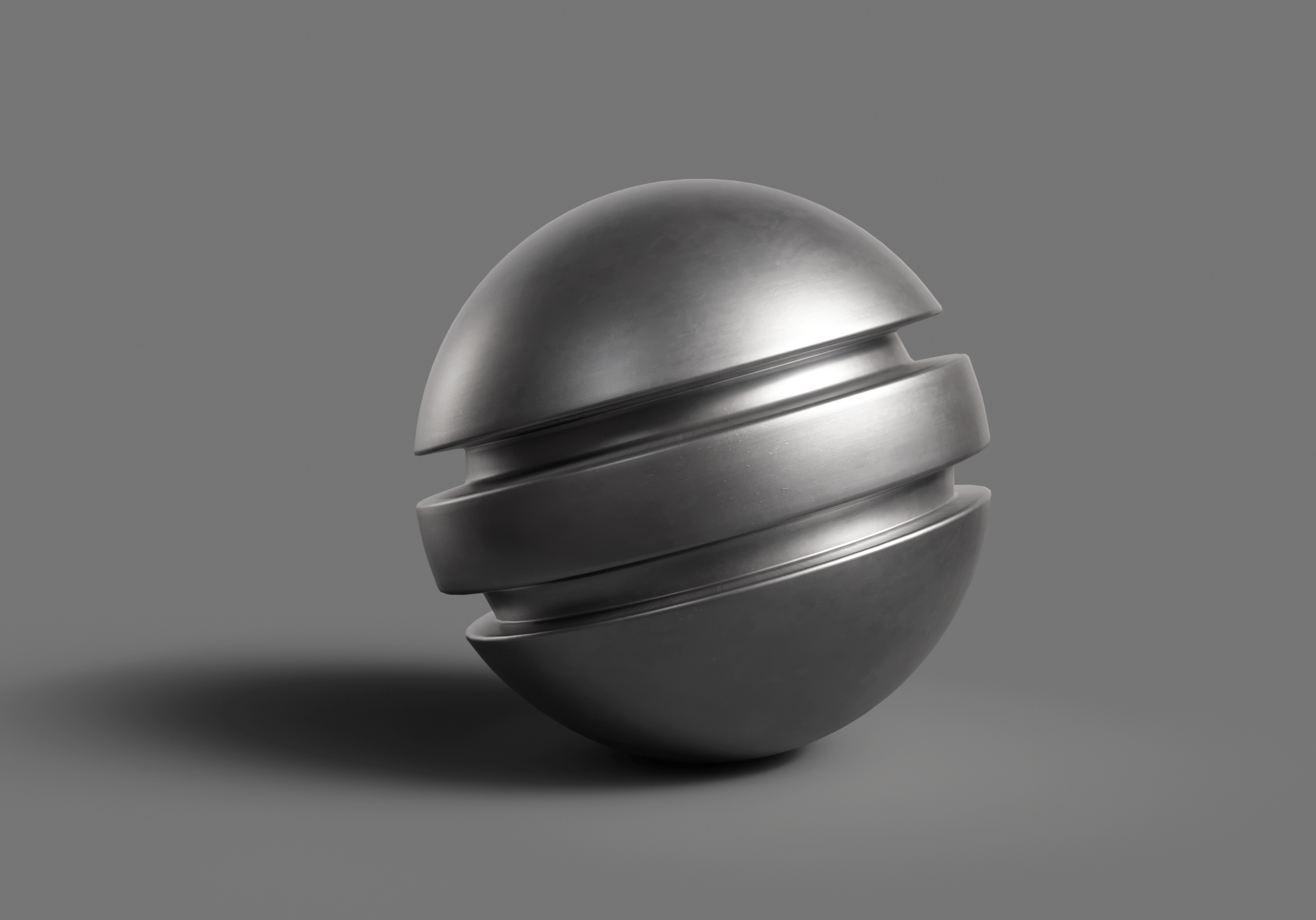
Carbon Steel
Carbon steel is a steel alloy containing carbon, and the varying levels of carbon determine the metal’s properties and characteristics. Manufacturers often use carbon steel because it is stronger and tougher than stainless steel, it is easily machined and welded, and it can be heat treated to improve its strength and durability. Energy-conscious manufacturers also choose carbon steel because it requires less energy to produce than other metals and is easy to recycle. Carbon steel is commonly used to create small mechanical parts like nuts, bolts, and gears. It is also used for many infrastructure and transportation projects, like in the construction of railway tracks, bridges, and buildings.
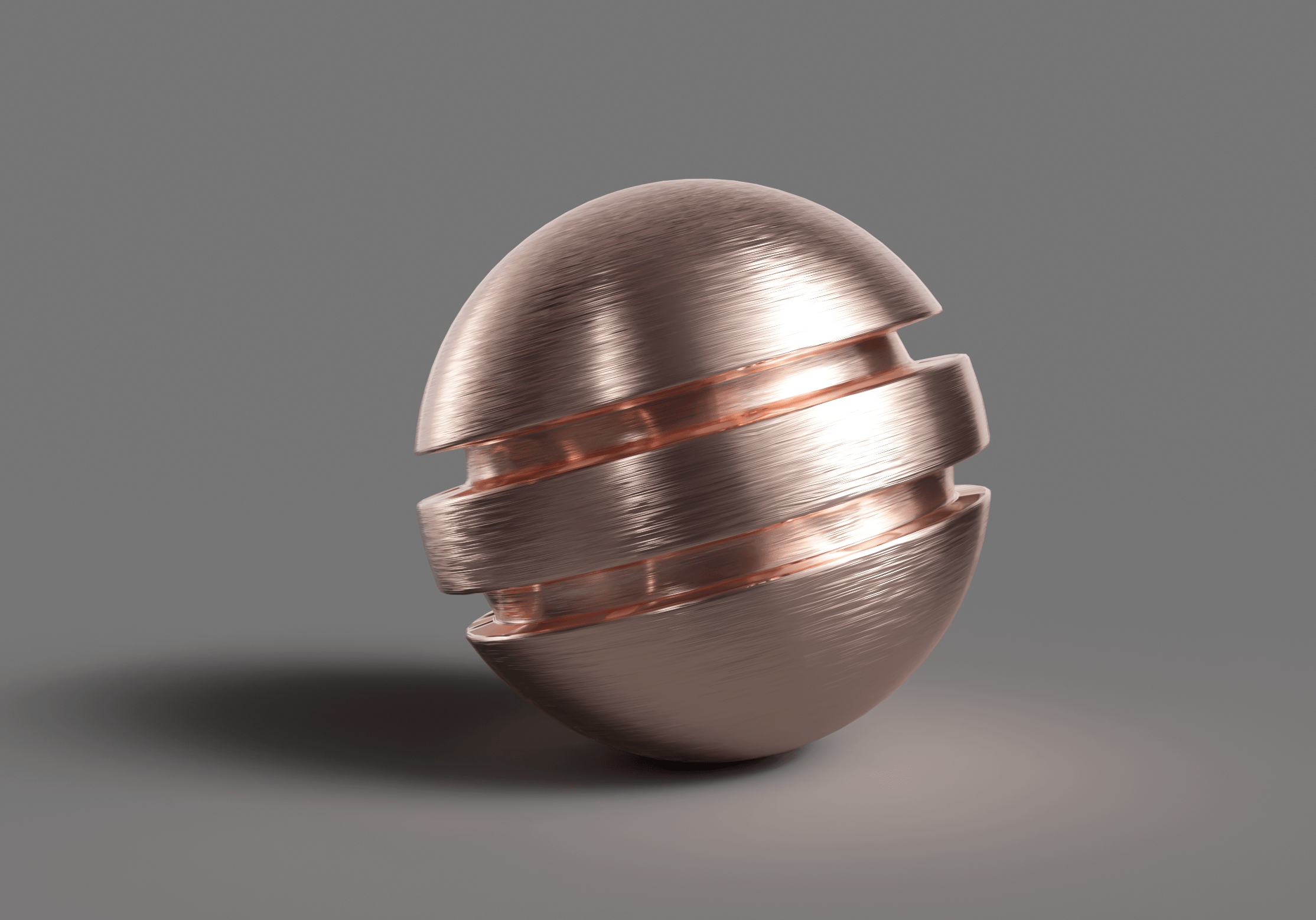
Copper
In its pure form, copper is a soft, malleable metal with high thermal and electrical conductivity. It is resistant to corrosion and bacteria, so it is ideal for long-term use in many different environments. Pure copper is commonly used for manufacturing electrical equipment and wires. The presence of other elements like tin, nickel, and zinc makes copper more machinable, and copper alloys such as bronze and brass are more common in machining components.
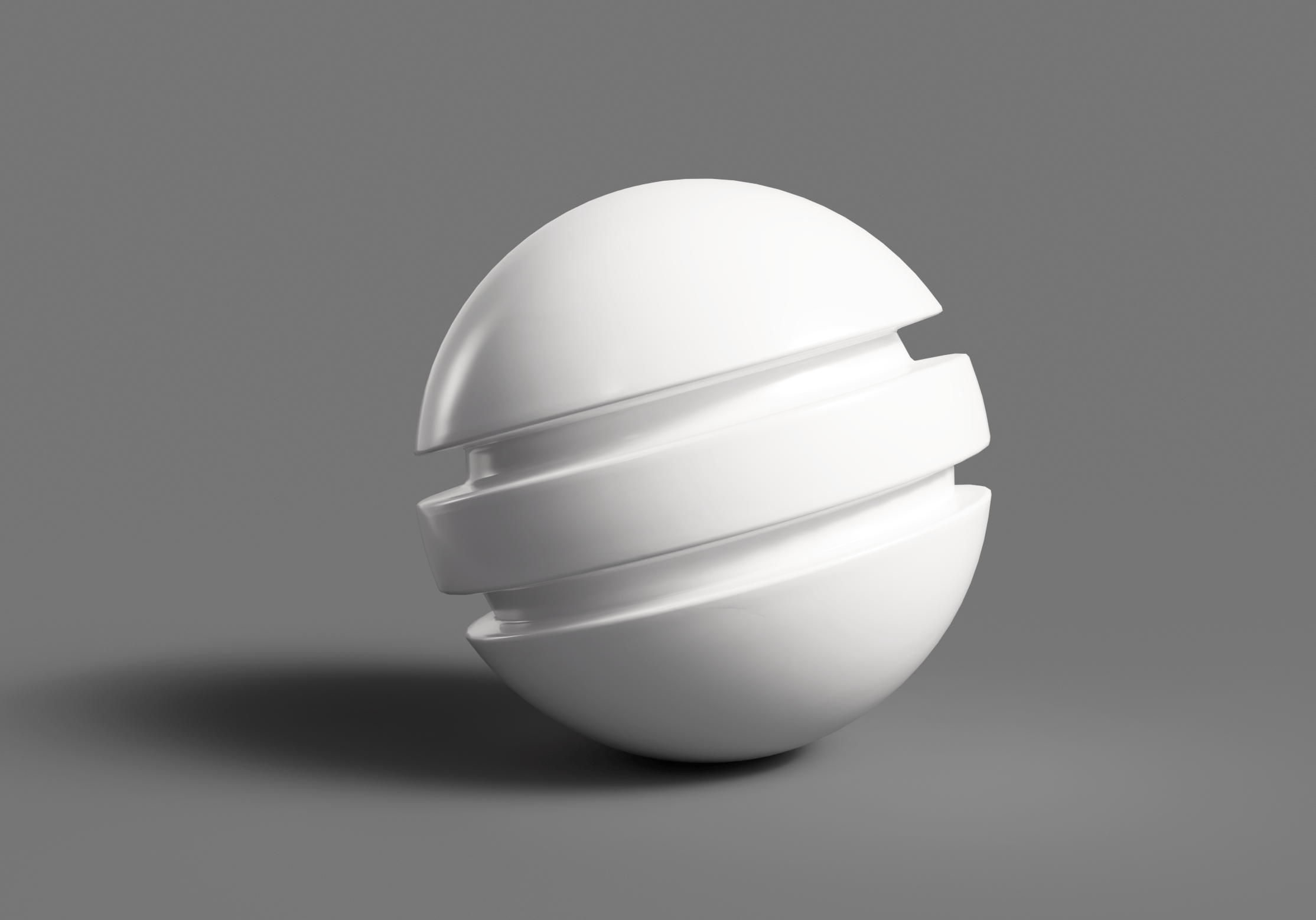
Plastics
CNC machining can be a preferable method when working with plastics because it is more precise than injection molding, can offer a smoother finish, and is more compatible with a wide range of materials. Plastics are often used when building prototypes or as a method to test designs. Nylon, a thermoplastic that becomes moldable when heated and then solidifies when cooled, is often used as a substitute for metals because it is tough, impact-resistant, and elastic. It is used to make electrical molding, mechanical parts, fabric, and fuel system components.
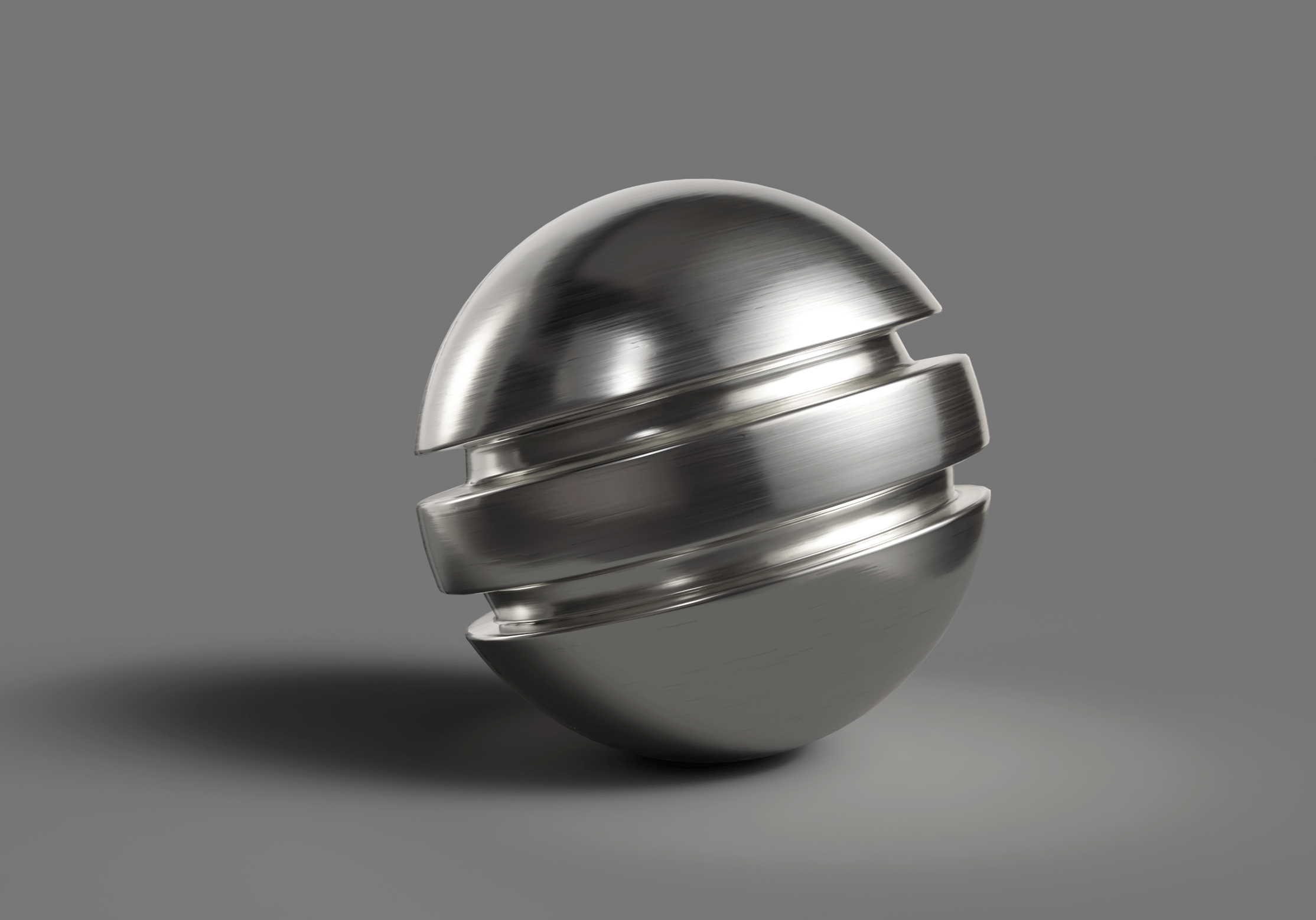
Stainless Steel
Stainless steel is an iron alloy, and it is a popular material for many CNC machining projects. It is highly weldable, strong, and durable, and it is resistant to corrosion and oxidation. Stainless steel has a wide variety of uses in various industries. It is found in industries that require corrosion resistance like aerospace, construction, and automotive, and it is also used to make medical parts and machining components.
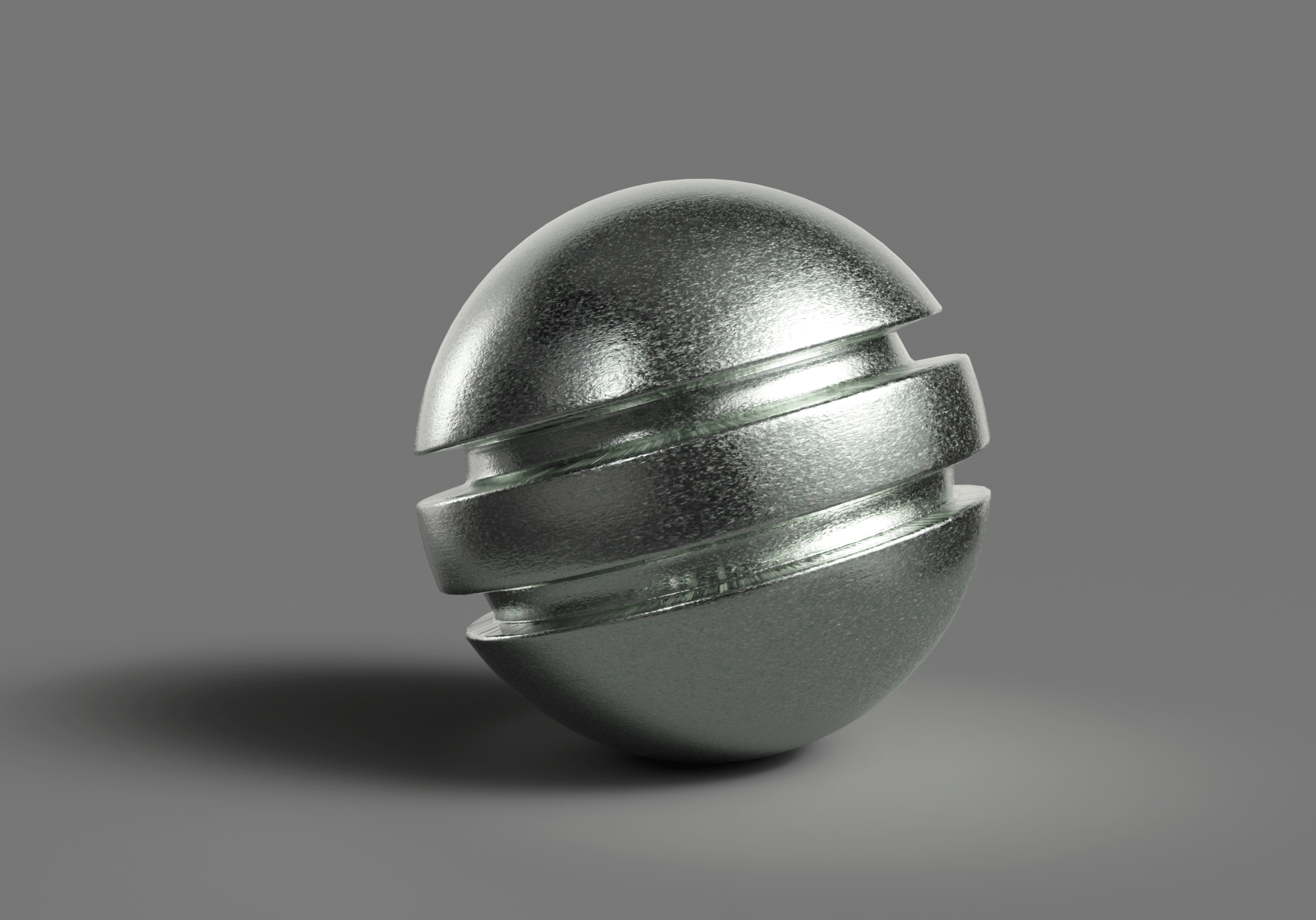
Titanium
Titanium is considered one of the strongest metals, and, although expensive when compared to other materials, it is one of the most popular metals used in CNC machining. That’s due to its strength, resistance to corrosion, ductility, and machinability. It is often used for demanding projects in aerospace, military, and industrial manufacturing. Because it is biocompatible (nontoxic and not rejected by the body) it has many medical uses, including surgical implants and medical instruments.
Applications
Many industries rely on CNC machines to provide precise, high-quality parts and products. Mass-produced products, prototypes, or parts where accuracy is everything can benefit from CNC machine production. Manufacturers can also use CNC machines to make custom tools and fixtures to aid in the production process.
Aerospace and Defense Industry
From military equipment to planes and rockets, aerospace and defense manufacturing partners provide some of the most crucial solutions affecting the world. Projects in this industry often require extremely tight tolerances and precise measurements. One mistake in a part could be detrimental to an entire project, aircraft, or piece of defense equipment.
Electrical Infrastructure and Energy
The energy and electrical infrastructure manufacturing industries often require smaller parts and exceptional accuracy. Quite often large batteries, energy storage units, and electrical components need to be surrounded and supported by panels or other solutions that can withstand exposure to outdoor elements. Manufacturing partners with precision CNC machining capabilities excel in these industries.
Medical Manufacturing
Details can be the difference between life and death in medical manufacturing, so the ability to create quality parts with precision is imperative. CNC software allows engineers to see all dimensions and details of a part before it’s made, providing exceptional verification and quality control. CNC machines aid in the creation of medical device components, surgical instruments, and patient monitoring and diagnostic equipment, among other products in the medical industry.
Advantages
CNC machines provide an extremely high level of repeatability, precision, and speed compared to traditional mills and lathes. They offer increased productivity for repetitive production and a safer environment.
Safety
While there are some operators involved in the process of CNC machining, they remain at a distance when sharp, fast-moving tools are in use. CNC machines are highly functional, and many can change tools on their own, making the need for human interaction less significant. Gates surround parts of the machine when they are in motion to keep operators at a safe distance. The machines are made to not have to be handled.
Speed
CNC machines offer repeated results at a fast pace, meaning they can produce the same part over again quickly. They can run all day and night, for hours on end, without tiring. After a test run of the product to make sure there are no flaws in the design, they can produce uniform, high-quality products to meet demand.
Precision
CNC machines are capable of achieving highly accurate and precise results without sacrificing quality. Once design instructions are loaded and the CNC is running, there is little opportunity for human error.
Conclusion
CNC machines are the solution to today’s manufacturing needs. The unmatched precision and versatility ensure the production of intricate, complex parts with minimal human intervention. They make it possible to create a range of work from rapid prototyping to large-scale runs while continuously producing consistent, high-quality items. CNC machines ensure ease and precision today while carving the way for tomorrow’s manufacturing practices.
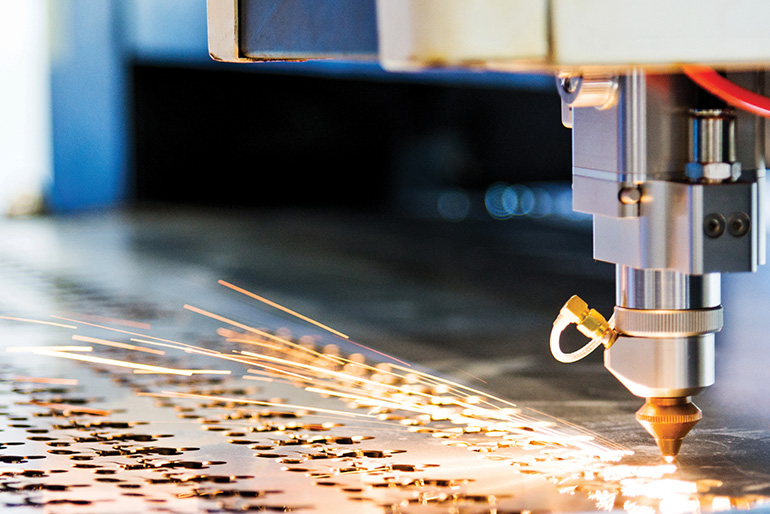
About Cadrex
Cadrex is one of the largest manufacturing partners in North America, with 20 facilities located in nine states and Mexico. As a leading custom mechanical solutions provider for the most innovative companies in the world today, we offer a unique breadth of capabilities and technical expertise that allow us to rapidly bring customer programs from concept to scale. In addition, our decades of specialized experience designing and manufacturing for information communication technology, warehouse automation & robotics, kiosk & gaming, aerospace & defense, renewable energy & electrical infrastructure, and medical sectors make us a trusted partner in our customer's supply chain.